In the world of product development and manufacturing, ensuring the quality of the end product is paramount. This is where Advanced Product Quality Planning, or APQP, comes into play. APQP is a structured approach to product quality planning that helps businesses ensure the delivery of high-quality products while minimizing risks and delays. In this blog, we’ll delve into the basics of Advanced Product Quality Planning, exploring its framework, key elements, tools, benefits, and the challenges businesses may encounter during its implementation.
Contents
The APQP Framework
The Advanced Product Quality Planning framework is a structured process encompassing distinct phases, each with specific objectives and tasks to ensure the successful development of high-quality products. These APQP phases are designed to guide organizations through the stages of quality planning, risk mitigation, and validation. By following the APQP phases, businesses can systematically address potential issues and deliver top-notch products to their customers while adhering to industry standards and regulations. These APQP phases include planning and definition, product design and development, process design and development, product and process validation, and feedback, assessment, and corrective action. Each phase plays a crucial role in the overall success of the APQP process, facilitating comprehensive quality planning and risk management throughout the product development journey.
APQP Tools and Techniques
APQP, or Advanced Product Quality Planning, employs a range of tools and techniques to ensure the successful development of high-quality products. These tools are crucial in identifying and mitigating risks throughout the product development process. Some key tools and techniques include Failure Mode and Effects Analysis (FMEA) for assessing potential failure modes and their consequences, control plans to outline necessary procedures and inspections, and Design Verification and Validation to confirm that the product design aligns with specified requirements and can be manufactured consistently. Additionally, Measurement Systems Analysis (MSA) is used to evaluate the reliability and accuracy of measurement systems during testing and inspection. Process Capability Studies are employed to assess the ability of a process to produce products within specified tolerance limits consistently. Finally, the Production Part Approval Process (PPAP) involves standardized documentation to demonstrate that customer engineering requirements are understood and consistently met.
These tools and techniques are essential for businesses looking to achieve consistent product quality, meet customer requirements, and adhere to industry standards and regulations. By integrating these tools into the APQP process, organizations can systematically address potential quality issues and ensure their products are not only high-quality but also in compliance with industry standards and customer expectations.
Benefits of Implementing APQP
Implementing Advanced Product Quality Planning (APQP) offers numerous benefits to organizations. Firstly, APQP significantly enhances product quality by systematically addressing potential issues and risks early in the development process. This proactive approach ensures that products meet or exceed customer requirements, resulting in higher customer satisfaction and an improved brand reputation. Moreover, APQP’s structured methodology helps reduce development time and costs. By identifying and mitigating risks during the initial phases of development, companies can minimize rework, delays, and associated expenses, leading to more efficient and cost-effective product development.
In addition to these advantages, APQP promotes improved communication and collaboration within organizations. The use of cross-functional teams and standardized documentation enhances communication and collaboration among different departments, resulting in a more streamlined and efficient development process. Lastly, APQP aids in ensuring compliance with industry standards and regulations, which is critical for businesses in various sectors, from automotive to healthcare.
Challenges in APQP Implementation
The implementation of Advanced Product Quality Planning (APQP) is not without its challenges. One significant challenge is resource allocation. Successful APQP implementation requires allocating the necessary resources, including skilled personnel, technology, and time. Ensuring that teams have the required tools and training to execute APQP processes effectively can be a demanding task for organizations.
Data collection and analysis can also pose a challenge during APQP implementation. Gathering and analyzing data throughout the APQP phases can be time-consuming and complex. Organizations need efficient data management and analysis systems to support decision-making and risk assessment. Furthermore, overcoming resistance to change and ensuring that employees are comfortable with new methods can be a challenge, particularly in the context of change management. APQP often requires a shift in organizational culture and processes, which can lead to resistance among team members. Ensuring everyone in the organization is on board with new APQP methodologies and committed to ongoing improvement is essential to overcoming these challenges.
Case Studies and Examples
To illustrate the real-world application of APQP, it’s beneficial to explore case studies and examples of businesses successfully implementing this quality planning approach. These stories demonstrate how APQP has led to improved product quality, reduced costs, and increased customer satisfaction in various industries.
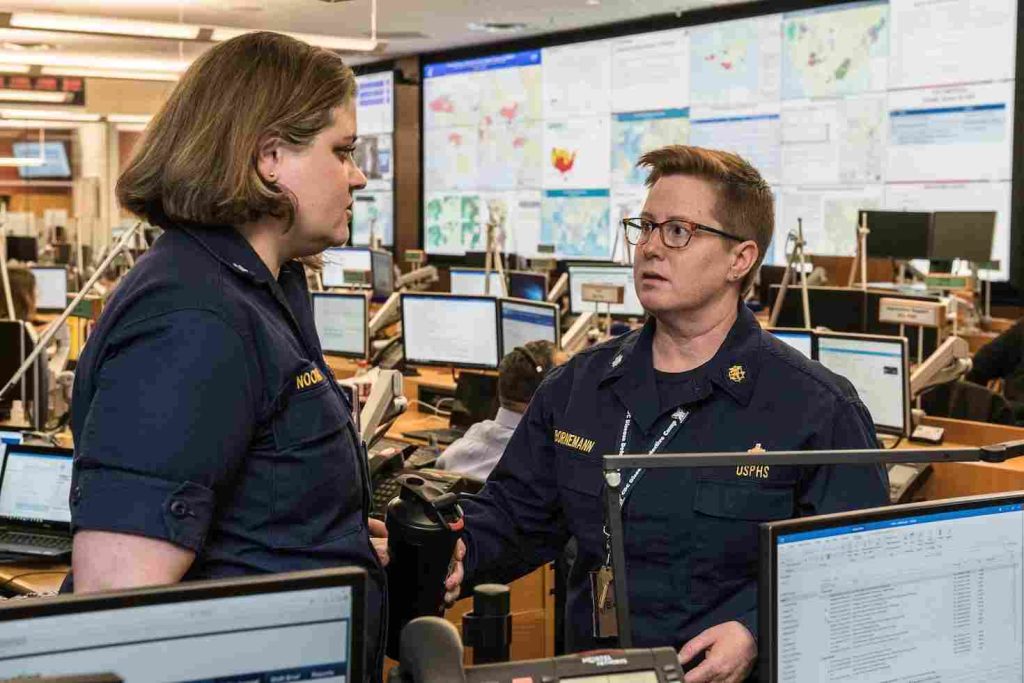
In the world of product development, quality planning is paramount. Advanced Product Quality Planning (APQP) is a structured and systematic approach that helps businesses ensure the delivery of high-quality products while minimizing risks and delays. By understanding the framework, key elements, tools, benefits, and potential challenges of APQP, businesses can successfully implement this approach to achieve remarkable product quality, customer satisfaction, and overall success in the competitive marketplace.